所谓冷压型焦法,是以粘结剂(也有不用粘结剂的)和惰性组分煤(或半焦粒)为原料,通过冷压工艺来製取冶金型焦的方法。
基本介绍
- 中文名:冷压型焦
- 外文名:formcoke from cold briquetting
- 含义:以粘结剂和惰性组分煤制冶金型焦
- 套用:冶金型焦的製备
冷压型焦简介
冷压型焦又有无粘结剂的冷压型焦和有粘结剂的冷压型焦之分。
无粘结剂的冷压型焦主要以泥煤、褐煤等低变质程度的煤为原料,靠料自身所含有的某种粘结成分,再藉助机械压力使之成型,成型后的块料再经炭化处理,便得冷压型焦。此工艺不需要外加粘结剂,故省材料、省设备,操作简单,成品率高且质量容易稳。但煤料的选择性很强且要求提供很高的成型压力(一般9.8~9.6×10Mpa),成型机械强度较大,国外多用冲压机或环压机代之。所以,如果改善成型方式,探索恰当的成型压力,研製有效的成型设备并使之广泛地用于其他煤种,是发展无粘结剂冷压型焦工艺的方向。
有粘结剂的冷压型焦工艺是以粉煤、半焦粉(乾馏碳)等为原料,同一定数量的粘结剂混合,在常温下以较低的压力(1.47~4.9×10Mpa)压製成型,型块经炭化处理即得型焦。
1969年,由日本京阪炼焦公司(Keihan Rentan)住友金属公司(Sumitomo)和西德迪弟尔公司(Didier-Kellogg)联合开发的DKS冷压型焦工艺,其型焦质量居世界领先地位。
该工艺用80%的非粘结煤、10%的碳素物料(如焦粉、石油焦)和10%的粘结煤。混合煤料粉碎至3毫米以下后,与煤焦油或硬沥青混合,并在100~2000℃压製成型,型块藉助大型料底炉在1300℃下炭化10h,即得冷压型焦。用于大型高炉(1300~2800m3)炼铁,可代替50%的冶金焦,并取得全料比约500kg/t、焦比低于450kg/t及高炉利用係数大于2t/m3d的良好效果。
我国50年代末就开展了冷压型焦的研究,曾利用广西老年褐煤半焦为原料,同少量焦油沥青作粘结剂,混合加压成型。型块作表面氧化处理,但型块强度较差,只能作无烟燃烧使用。龙北曾用无烟煤(85%)和沥青(15%)配合,採用两级粉碎(<3毫米粒级的占95%以上),再用蒸气加热混捏成型,型块经炭化处理后可在30立方米小高炉炼铁使用,但型焦的耐磨性和抗碎性比较差,平均焦比达1480千克/t,高炉吹损为300kg/t左右。我国冷压型焦质量较好的是以鞍山焦化耐火材料设计研究院与鞍山热能研究所为主研究的,在河南鹤壁钢铁厂生产的瘦煤冷压型焦流程。
冷压型焦原理
第一种方法是把煤(主要是褐煤)在高压下成型,得到的型块再进行炭化处理,以製取无烟燃料或型焦。此方法的原理是:在很高的成型压力下,煤粒紧紧地贴在一起,互相摩擦、挤压。由于压力很高,煤粒本身发热,变软,煤粒之间便容易结合在一起,最终而形成型煤,型煤经炭化处理后成为型焦。
第二种方法是把惰性组分煤与一定配比的粘结剂充分混匀后,加热到比粘结剂的软化点稍高-—点的温度下压型,最后把型煤通过直接炭化或氧化后炭化,製得无烟燃料或型焦。
从第二种方法可以看到,製取冷压焦要经过混合、热融压型和型块处理等三个过程。在粘结组分与惰性组分混合过程巾,粘结组分均匀地分布于惰性组分之间。混合物的温度处于粘结组分的软化温度时,粘结组分便会软化熔融呈流动性,并吸附在惰性组分的表面,形成一层粘结组分膜,使整个混合物呈塑性状态。这个膜的结合强度取决于粘结组分的附着力和内聚力。粘结组分被惰性组分充分吸附时,结合强度大。如果吸附不足,则结合强度差。当混合物在具有比粘结组分软化点稍高一点的温度下进行压型时,惰性组分之间被压紧,粘结组分更加均匀地几乎以同样的厚度覆盖在惰性组分的表面。型块脱模后,粘结组分迅速凝聚,使得型块具有冷态的强度。生型块的冷强度取决于粘结组分的内聚力、惰性组分的结构强度和粘结组分与惰性组分分界面的结合强度。为了製取冶金用的冷压型焦,生型块必须进行最终炭化处理,特别要进行高温炭化。因为在高温炭化时,一方面惰性组分进行热分解和缩聚反应,表面结构不断改变,温度愈高,碳核排列愈紧密,结构强度增加;另一方面,粘结组分也进行裂解和缩聚,芳构化程度增大,在高温下参与碳核的重新排列,最后形成焦炭结构,即形成冷压型焦。
冷压型焦工艺流程
无粘结剂冷压型焦
将无粘结剂冷压型煤进一步焦化,即得无粘结剂冷压型焦。这种工艺主要用于褐煤生产型焦。如:德国将丰富的软褐煤资源炼製型焦,作为民用或工业燃料。其主要工艺流程见下图。
将破碎后小于1mm、挥发分46%左右、灰分小于6%、水分50%~55%的年轻褐煤,用半封闭式胶带输送机送入旋转乾燥机进行乾燥,至水分10%左右、温度90℃,再用半封闭式刮板输送机送至型煤厂用冲压机成型。成型后的型煤送至高温炼焦炉进行焦化。该焦结炉是一种集乾燥、焦化和乾法熄焦为一体的3段连续操作竖炉,结焦温度为1050~1100℃,结焦时间为11~15h。
这种褐煤高温炼焦炉,由于炭化室是外热式和乾法熄焦,生产的褐煤型焦及煤气质量都比一般内热式焦炉好;焦炉的乾燥段效率高并採用连续程式控制,因此耗热量也比一般室式焦炉低,焦结炉自用煤气仅占自产煤气的22%~27%。
粘结剂冷压型焦
将粘结剂冷压型煤进一步焦化即得粘结剂冷压型焦。根据所用原料煤不同,粘结剂冷压型焦工艺又可分为两段法流程和一段法流程。其中两段法流程为:以高挥发分、低变质程度煤(如年老褐煤、长焰煤、气煤)为原料进行低温乾馏(第一段),生产固体焙烧物(半焦)和焦油。再将两者混合压製成型,型煤经高温焦化製成型焦(第二段)。美国的FMC法和罗马尼亚的ICEM法均属此种流程。一段法流程为:以低挥发分、高变质程度的瘦煤、贫煤、无烟煤为主要原料煤,配加少量粘结煤,直接加粘结剂压製成型,再经高温焦化製成型焦。日本的DKS法和法国的HBNPC法均属此种流程。

世界各国粘结剂冷压型焦工艺,如上表所示。其中DKS型焦工艺是由德国迪地尔炼焦工程公司(Didier Kel.1099)、日本京阪炼炭公司(Keihan Rentan)和住友金属工业公司(Sumitomo)于1969年联合研製开发的。冷压型焦质量居世界领先地位。1971年在大阪建立了一座4.8万t/a半工业试验装置,次年用生产的型焦在1350m3高炉试验取得满意的结果。1977年建成工业化的型焦厂。该工艺使用的原料煤主要是非粘结煤。其中粘结煤为5%~10%,不粘结煤为70%~80%,焦粉或石油焦10%。原料煤混合后粉碎至<3mm,配入10%的煤焦油沥青作粘结剂,用蒸汽加热至200℃压製成型煤。其水分5%~7%,挥发分小于30%,装入斜底外热式焦炉,在1200~1300℃的条件下焦化10h,所得型焦沿斜底靠自重排出。工艺流程下图所示。
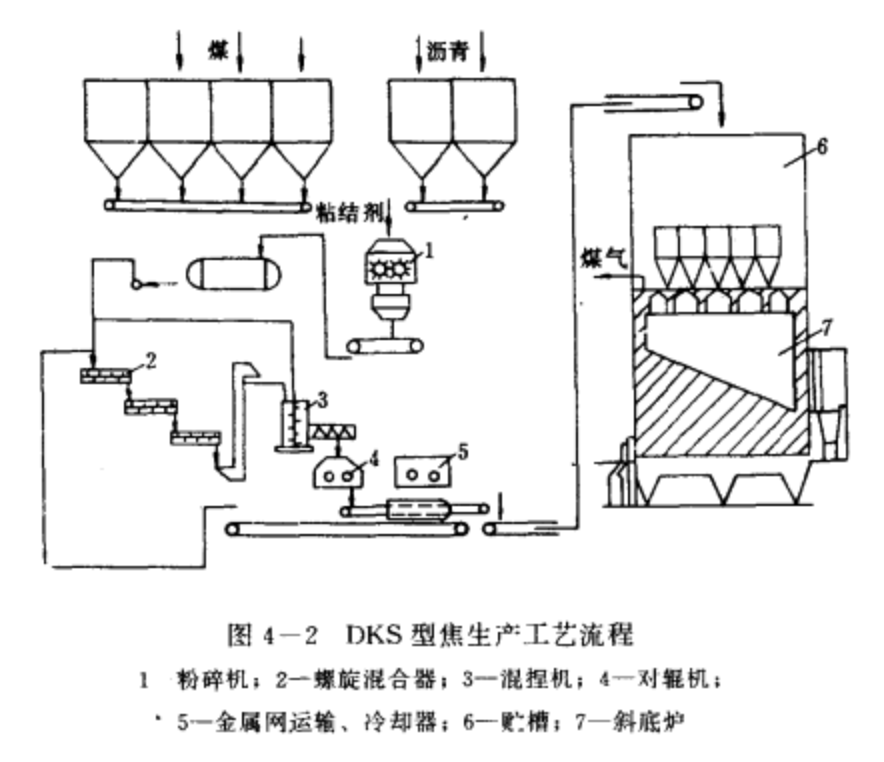
用DKS型焦在大型高炉(1300~2800m3)内代替50%的冶金焦,曾进行过6次炼铁试验,取得全燃料比约每吨铁500kg,高炉利用係数大于2t/m3·d,焦比<450kg/t的良好效果。结果表明:技术经济指标可同常规室式焦炉相媲美,而基建费用比室式焦炉低5%~10%,该工艺最大优点是能大量利用不粘结煤,型焦质量不亚于高质量冶金焦。