丙烷预冷混合製冷剂液化工艺是最常用的天然气液化工艺,该工艺结合了级联式液化流程与混合製冷剂液化流程的优点,既高效又简单,世界上80%以上的基本负荷型天然气液化装置採用了此流程。
由于实际情况中原料气的入口压力、温度、组分均存在变化的可能,需要针对工艺的原料气敏感性进行动态仿真分析。通过分别添加原料气压力、温度、组分的扰动,得到了各个工艺系统的动态回响。结果表明:当丙烷预冷混合製冷剂液化工艺分别存在原料气压力、温度、组分扰动时,各个系统均能在一段时间后重新恢复稳定,稳定时间为20~250min。验证了丙烷预冷混合製冷剂液化工艺在原料气入口条件扰动时的稳定性和可靠性。
基本介绍
- 中文名:丙烷预冷
- 外文名:Propane pre-cooling
- 描述:天然气液化工艺
- 套用:混合製冷剂液化工艺
- 学科:能源科学
概念
丙烷预冷混合製冷剂分离液化可以採用一次分离或二次分离。二次分离液化流程与一次分离液化流程相比,系统多了一个分离器、 一个液相节流阀、一个换热器,但两者换热面积相差不大。二次分离流程工艺计算却複杂了很多, 一次工艺计算需几十个机时。增加一个分离器的目的是减少混合製冷剂的预冷热负荷,即一次分离后的气相经冷却后为气、 液两相,为使液相即刻节流产冷而增加二次分离器,分离出的液相经节流而产冷,余气再经过过冷器冷却、 液化,再节流产冷。
丙烷预冷
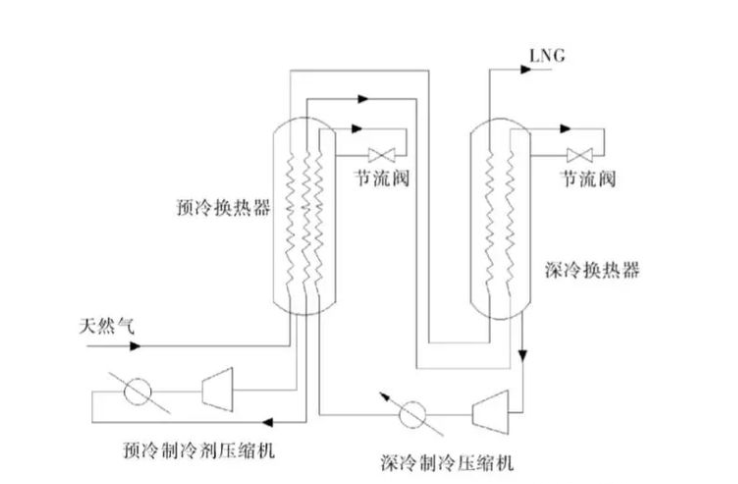
丙烷预冷混合製冷剂二次分离液化工艺计算
进入21世纪,我国天然气事业得到飞速发展,天然气已经广泛套用于各行各业。天然气长输管道输送项目建设周期长、投资巨大,靠天然气长输管道输送供气,下游天然气市场供不应求,部分地区、城市、大型用户用气高峰季节出现气荒。近年来,天然气( 煤层气) 液化项目纷纷上马,天然气(煤层气)液化工艺能耗指标优劣取决于製冷循环工艺,丙烷预冷混合製冷剂分离液化工艺是混合製冷循环工艺之一, 也是国外大型天然气液化厂普遍採用的液化工艺。
图 1 丙烷预冷混合製冷剂二次分离液化工艺流程
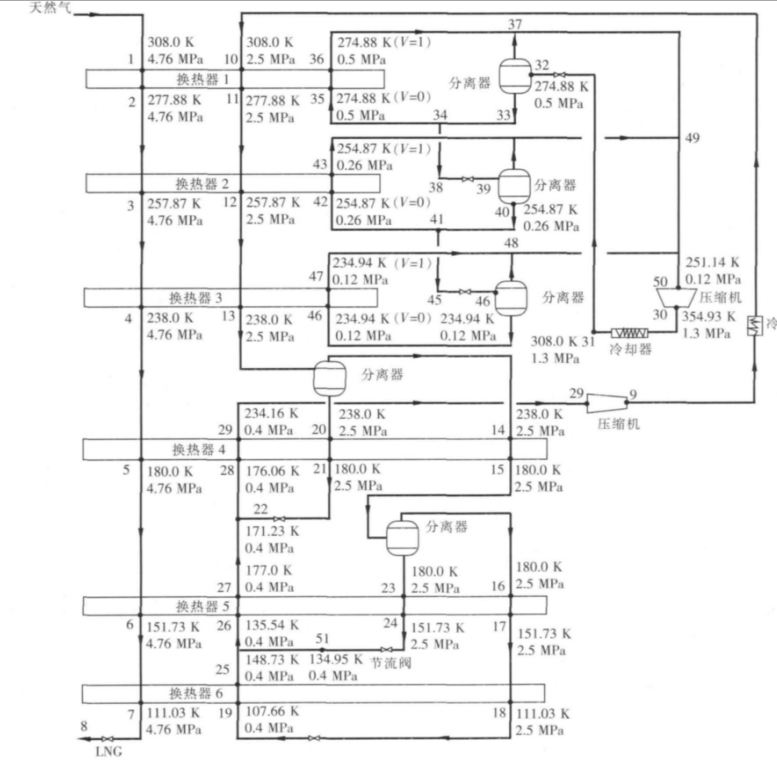
计算的目的
(1)选择製冷剂;
(2)求循环量最小的製冷剂配比;
(3)求混合製冷剂压缩机最佳出口压力;
(4)求天然气压缩机最佳出口压力。
工艺流程
丙烷预冷混合製冷剂二次分离液化工艺流程见图1。此流程适于大规模天然气液化生产。天然气液相节流阀后,气相分率V = 0,丙烷循环流程同一次分离流程,各节点参数也相同。计算结果见图1。
天然气的最佳压力
以p1=4.5~5.5MPa,按上述过程求最佳天然气压力。天然气的压力越高,其需冷量越小,则混合製冷剂的循环量越小,混合製冷剂压缩机的功率越小,然而天然气压力越高,天然气压缩机的功率越大。经试算,天然气的压力约为4.8MPa 时,综合能耗处于较低值。
丙烷预冷製冷剂液化工艺原料气敏感性分析
液化天然气由于其本身的优越性,近年来得到了快速发展。天然气液化后便于进行经济可靠的运输,提高储存效率和安全保证,有利于城市负荷的调节,并且对环境效益显着。在天然气液化工艺中,20世 纪70年代后期 和80年代初期,美国空气液化公司成功开发出丙烷预冷的混合製冷剂液化技术,在大型液化天然气工厂得到广泛的套用。到2003年,世界上液化天然气产量的85%使用丙烷预冷的混合製冷剂液化工艺,其中预冷段採用丙烷製冷剂,液化段採用混合製冷剂,很好地提高了液化率和製冷剂循环效率。
天然气液化装置运行时,外界条件是时刻变化的,在存在扰动的情况下系统运行的稳定性是选择液化工艺的一个重要因素,而动态仿真是验证液化工艺稳定性的重要手段。国外对液化工艺的动态仿真起步较早,相关文献建立了液化工艺中主要设备的动态模型并对液化工艺进行了动态仿真,并对单级混合製冷剂液化工艺和多级混合製冷剂液化工艺进行了简单的动态仿真。挪威科技大学对混合製冷剂液化工艺的动态仿真做了大量的工作,以挪威建设的大型天然气液化装置为基础建立了混合製冷剂液化工艺中主要设备的动态模型,并对级联式混合製冷剂液化工艺、单级混合製冷剂液化工艺和多级混合製冷剂液化工艺进行了动态仿真及控制方式的研究,但是仅仅局限于天然气流量扰动时的动态仿真,没有进行存在其他扰动变化时的动态仿真。相对来说国内对混合製冷剂的动态仿真起步较晚,主要集中在上海交通大学、哈尔滨工业大学。上海交通大学从20世纪90年代开始从事天然气液化相关技术的研究,主要是採用数值模拟方法进行液化工艺的分析和研究,哈尔滨工业大学主要针对混合製冷剂循环进行动态仿真研究、流程操作特性和适应性研究。
由于实际情况中原料气的入口压力、温度、组分均存在变化的可能,需要针对丙烷预冷混合製冷剂液化工艺进行动态仿真,并对其原料气敏感性进行分析。通过分别添加原料气压力、温度、组分的扰动,得到了混合製冷剂、丙烷製冷剂、原料气3个工艺系统的动态回响,从而验证丙烷预冷混合製冷剂液化工艺在原料气入口条件扰动时的稳定性和可靠性。
丙烷预冷混合製冷剂液化工艺模型建立
利用AspenHSYSY建立动态仿真模型,如图1所示。动态仿真时,首先根据丙烷预冷混合製冷剂液化工艺建立流程的稳态模型,并以稳态模型的结果作为建立动态模型的初值,然后根据实际中的设备参数及边界条件进行动态参数的设定,并增加PID控制器。动态模型採用压力驱动的方式实现,模型中的流量通过阻力和压力差计算,因此模型中需要设定各个压缩机的功率和效率以及阀门等阻力件的开度和流量係数,从而得到合理的流量。
图1 丙烷预冷混合製冷剂流程图
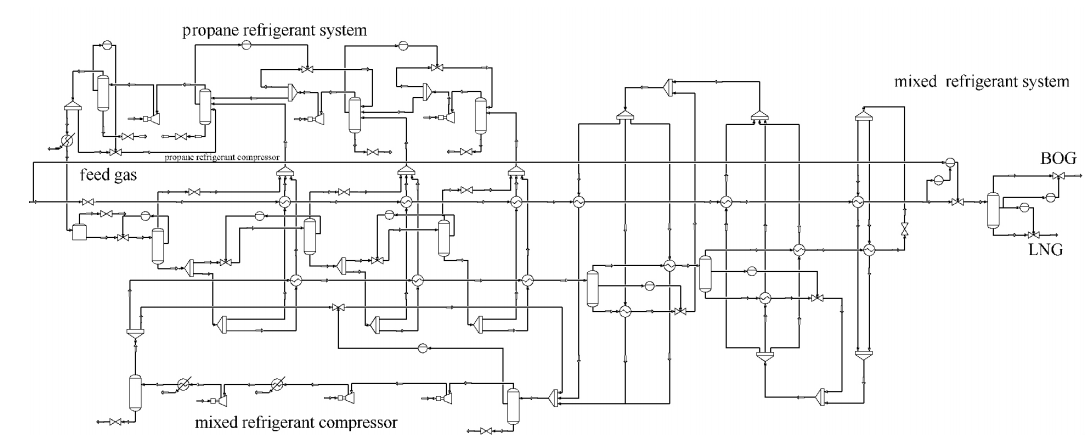
研究结论
通过动态仿真的方式给丙烷预冷混合製冷剂液化工艺流程分别添加原料气入口压力、温度、组分的扰动,获得混合製冷剂、丙烷製冷剂、原料气3个工艺系统的回响。当原料气压力扰动时,混合製冷剂系统需要160~250min恢复稳定,丙烷製冷剂系统需要160min、左右恢复稳定,原料气系统需要160min左右恢复稳定;当原料气温度扰动时,混合製冷剂系统需要60~80min恢复稳定,丙烷製冷剂系统需要20~30min恢复稳定,原料气系统需要20~80min恢复稳定;当原料气组气扰动时,混合製冷剂系统需要150min左右恢复稳定,丙烷製冷剂系统需要140min左右恢复稳定,原料气系统需要30~160min恢复稳定。验证了丙烷预冷混合製冷剂液化工艺在原料气入口条件扰动时的稳定性和可靠性。而且原料气压力和组分的扰动对系统影响较大,系统恢复稳定所需时间教长;原料气温度的扰动对系统影响相对较小,系统恢复稳定所需时间较短。