塑胶在注塑机加热料筒中塑化后,由柱塞或往复螺桿注射到闭合模具的模腔中形成製品的塑胶加工方法。此法能加工外形複杂、尺寸精确或带嵌件的製品,生产效率高。大多数热塑性塑胶和某些热固性塑胶(如酚醛塑胶)均可用此法进行加工。用于注塑的物料须有良好流动性,才能充满模腔以得到製品。 20世纪70年代以来,出现了一种带有化学反应的注射成型,称为反应注射成型,发展很快。
基本介绍
- 中文名:注射成型
- 优点:生产效率高
- 用于:大多数热塑性塑胶某些热固性塑胶
- 主要装置:注塑机
简介
注射成型是将注射机熔融的塑胶,在柱塞或螺桿推力作用下进入模具,经过冷却获得製品的过程。
主要装置
注塑机
即注射成型机(见彩图)。由注射装置、合模装置和注塑模具三部分组成。注塑机的规格有两种表示法:一种是每次最大注射体积或重量,另一种是最大合模力。注塑机其他主要参数为塑化能力、注塑速率和注射压力。
立式注塑机
卧式注塑机
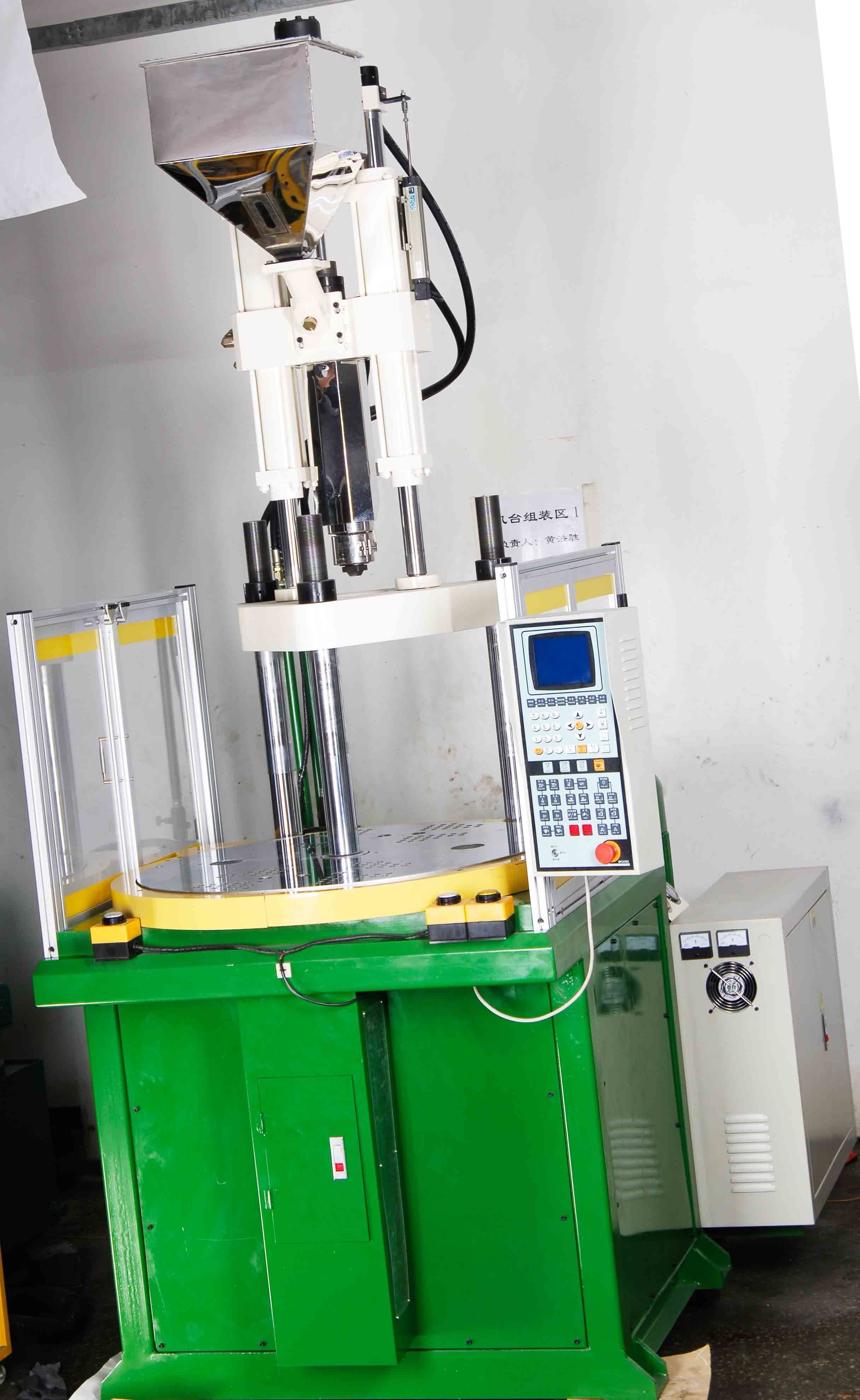
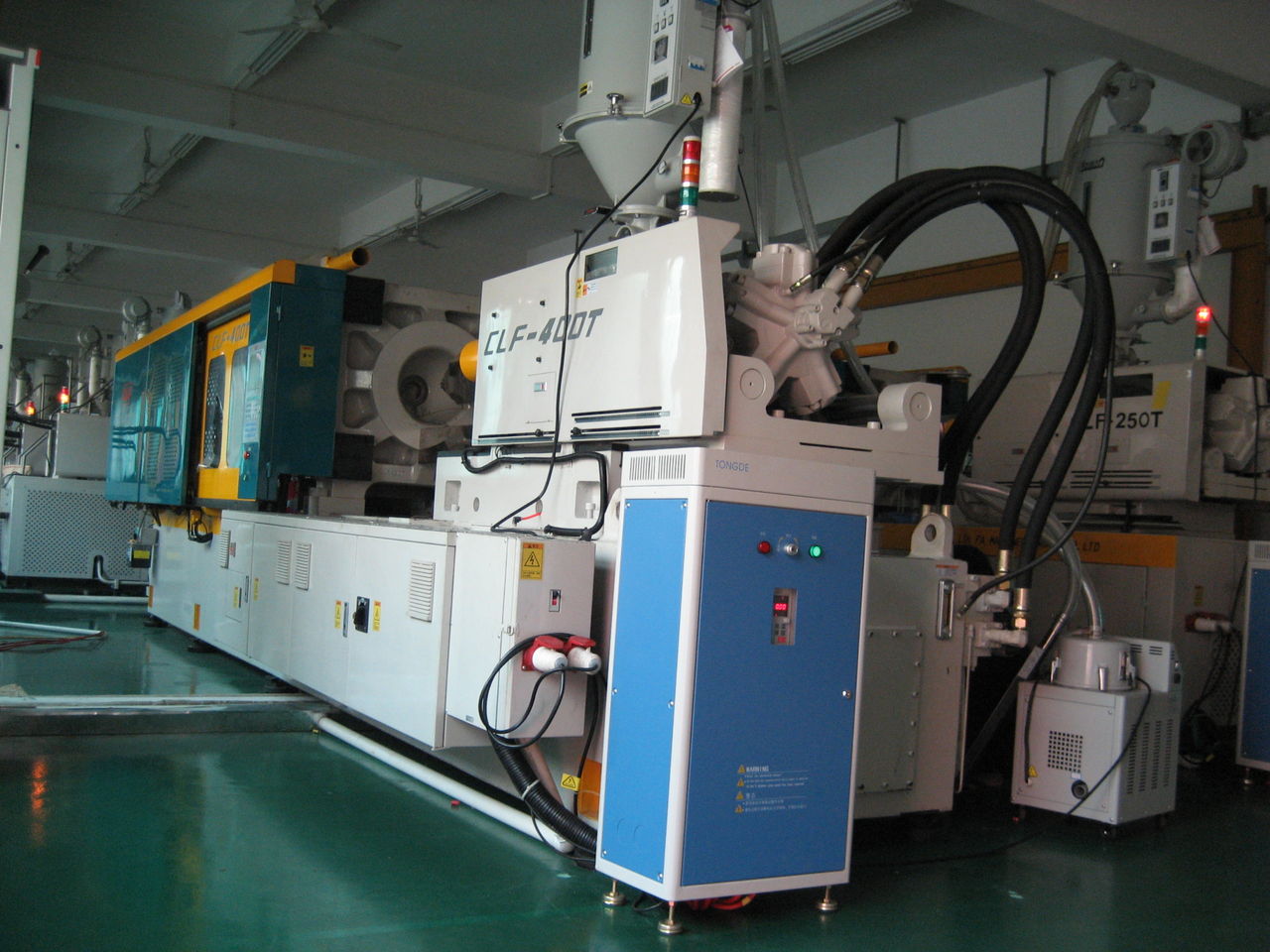
注射装置
注塑机的主要部分。将塑胶加热塑化成流动状态,加压注射入模具。注射方式有柱塞式、预塑化式和往复螺桿式。后者(图1)具有塑化均匀、注射压力损失小、结构紧凑等优点,套用较广泛。
合模装置
用以闭合模具的定模和动模,并实现模具开闭动作及顶出成品。
注塑模具
简称注模(图2)。它由浇注系统、成型零件和结构零件所组成。①浇注系统是指自注射机喷嘴到型腔的塑胶流动通道;②成型零件是指构成模具型腔的零件,由阴模、阳膜组成;③结构零件,包括导向、脱膜、抽芯、分型等各种零件。模具分为定模和动模两大部分,分别固定于合模装置之定板和动板上,动模随动板移动而完成开闭动作。模具根据需要可加热或冷却。
注塑车间

操作方法
因加工物料而异。热塑性塑胶的注射成型包括加料、塑化、注射、保压、冷却、脱模等过程。热固性塑胶和橡胶的成型也包括同样过程,但料筒温度 较热塑性塑胶的低,注射压力却较高,模具是加热的,物料注射完毕在模具中需经固化或硫化过程,然后趁热脱膜。
注射成型是指有一定形状的模型,通过压力将融溶状态的胶体注入摸腔而成型,工艺原理是:将固态的塑胶按照一定的熔点融化,通过注射机器的压力,用一定的速度注入模具内,模具通过水道冷却将塑胶固化而得到与设计模腔一样的产品。
注射成型(注塑)是使热塑性或热固性模塑胶先在加热料筒中均匀塑化,而后由柱塞或移动螺桿推挤到闭合模具的模腔中成型的一种方法。
注射成型几乎适用于所有的热塑性塑胶。注射成型也成功地用于成型某些热固性塑胶。注射成型的成型周期短(几秒到几分钟),成型製品质量可由几克到几十千克,能一次成型外形複杂、尺寸精确、带有金属或非金属嵌件的模塑品。因此,该方法适应性强,生产效率高。
注射成型用的注射机分为柱塞式注射机和螺桿式注射机两大类,由注射系统、锁模系统和塑模三大部分组成;其成型方法可分为:
(1) 排气式注射成型。排气式注射成型套用的排气式注射机,在料筒中部设有排气口,亦与真空系统相连线,当塑胶塑化时,真空泵可将塑胶中合有的水汽、单体、挥发性物质及空气经排气口抽走;原料不必预乾燥,从而提高生产效率,提高产品质量。特别适用于聚碳酸酯、尼龙、有机玻璃、纤维素等易吸湿的材料成型。
(2) 流动注射成型。流动注射成型可用普通移动螺桿式注射机。即塑胶经不断塑化并挤入有一定温度的模具型腔内,塑胶充满型腔后,螺桿停止转动,借螺桿的推力使模内物料在压力下保持适当时间,然后冷却定型。流动注射成型克服了生产大型製品的设备限制,製件质量可超过注射机的最大注射量。其特点是塑化的物件不是贮存在料筒内,而是不断挤入模具中,因此它是挤出和注射相结合的一种方法。
(3) 共注射成型。共注射成型是採用具有两个或两个以上注射单元的注射机,将不同品种或不同色泽的塑胶,同时或先后注入模具内的方法。用这种方法能生产多种色彩和(或)多种塑胶的複合製品,有代表性的共注射成型是双色注射和多色注射。
(4) 无流道注射成型。模具中不设定分流道,而由注射机的延伸式喷嘴直接将熔融料分注到各个模腔中的成型方法。在注射过程中,流道内的塑胶保持熔融流动状态,在脱模时不与製品一同脱出,因此製件没有流道残留物。这种成型方法不仅节省原料,降低成本,而且减少工序,可以达到全自动生产。
(5)反应注射成型。反应注射成型的原理是将反应原材料经计量装置计量后泵入混合头,在混合头中碰撞混合,然后高速注射到密闭的模具中,快速固化,脱模,取出製品。它适于加工聚氨酯、环氧树脂、不饱和聚酯树脂、有机硅树脂、醇酸树脂等一些热固性塑胶和弹性体。主要用于聚氨酯的加工。
(6) 热固性塑胶的注射成型。粒状或团状热固性塑胶,在严格控制温度的料筒内,通过螺桿的作用,塑化成粘塑状态,在较高的注射压力下,物料进入一定温度範围的模具内交联固化。热固性塑胶注射成型除有物理状态变化外,还有化学变化。因此与热塑性塑胶注射成型比,在成型设备及加工工艺上存在着很大的差别。下表比较了热固性与热塑性塑胶注射成型的差别。
热固性与热塑性塑胶注射成型条件的比较
工艺条件 | 热固性塑胶 | 热塑性塑胶 |
料筒温度 | 温度低,95℃以下,温度控制严格 | 温度高,150℃以上,温度控制不严格 |
料筒中停留时间 | 短 | 较 长 |
料筒加热方式 | 液体介质(水、油) | 电加热 |
模具温度 | 150一200℃ | 100℃以下 |
注射压力 | 100-200MPa | 35-140MPa |
注射量 | 注射量较小,料筒前部余料很小 | 注射量较大,料筒前部余料较多 |
注意事项
注塑成型是一门工程技术,它所涉及的内容是将塑胶转变为有用并能保持原有性能的製品。注射成型的重要工艺条件是影响塑化流动和冷却的温度,压力和相应的各个作用时间。
温度控制
1、料筒温度:注射模塑过程需要控制的温度有料筒温度,喷嘴温度和模具温度等。前两程温度主要影响塑胶的塑化和流动,而后一种温度主要是影响塑胶的流动和冷却。每一种塑胶都具有不同的流动温度,同一种塑胶,由于来源或牌号不同,其流动温度及分解温度是有差别的,这是由于平均分子量和分子量分布不同所致,塑胶在不同类型的注射机内的塑化过程也是不同的,因而选择料筒温度也不相同。
2、喷嘴温度:喷嘴温度通常是略低于料筒最高温度的,这是为了防止熔料在直通式喷嘴可能发生的“流涎现象”。喷嘴温度也不能过低,否则将会造成熔料的早凝而将喷嘴堵死,或者由于早凝料注入模腔而影响製品的性能。
3、模具温度:模具温度对製品的内在性能和表观质量影响很大。模具温度的高低决定于塑胶结晶性的有无、製品的尺寸与结构、性能要求,以及其它工艺条件(熔料温度、注射速度及注射压力、模塑周期等)。
压力控制
注塑过程中压力包括塑化压力和注射压力两种,并直接影响塑胶的塑化和製品质量。
1、塑化压力:(背压)採用螺桿式注射机时,螺桿顶部熔料在螺桿转动后退时所受到的压力称为塑化压力,亦称背压。这种压力的大小是可以通过液压系统中的溢流阀来调整的。在注射中,塑化压力的大小是随螺桿的转速都不变,则增加塑化压力时即会提高熔体的温度,但会减小塑化的速度。此外,增加塑化压力常能使熔体的温度均匀,色料的混合均匀和排出熔体中的气体。一般操作中,塑化压力的决定应在保证製品质量优良的前提下越低越好,其具体数值是随所用的塑胶的品种而异的,但通常很少超过20㎏/c㎡。
2、注射压力:在当前生产中,几乎所有的注射机的注射压力都是以柱塞或螺桿顶部对塑胶所施的压力(由油路压力换算来的)为準的。注射压力在注塑成型中所起的作用是,克服塑胶从料筒流向型腔的流动阻力,给予熔料充模的速率以及对熔料进行压实。
注射压力分射胶压力和保压压力,通常是1到4段射胶压力+1到3段保压压力,一般保压压力小于射胶压力,根据实际使用的塑胶材料进行调节,以达到佳的物理性能,外观和尺寸要求。
成型周期
完成一次注射模塑过程所需的时间称成型周期,也称模塑周期。它实际包括以下几部分:
成型周期:成型周期直接影响劳动生间率和设备利用率。因此,在生产过程中应在保证质量的前提下,儘量缩短成型周期中各个有关时间。在整个成型周期中,以注射时间和冷却时间最重要,它们对製品的质量均有决定性的影响。注射时间中的充模时间直接反比于充模速率,生产中充模时间一般约为3~5秒。
注射时间中的保压时间就是对型腔内塑胶的压力时间,在整个注射时间内所占的比例较大,一般约为20~120秒(特厚製件可高达5~10分钟)。在浇口处熔料封冻之前,保压时间的多少,对製品尺寸準确性有影响,若在以后,则无影响。保压时间也有最惠值,已知它依赖于料温,模温以及主流道和浇口的大小。如果主流道和浇口的尺寸以及工艺条件都是正常的,通常即以得出製品收缩率波动範围最小的压力值为準。冷却时间主要决定于製品的厚度,塑胶的热性能和结晶性能,以及模具温等。冷却时间的终点,应以保证製品脱模时不引起变动为原则,冷却时间性一般约在30~120秒钟之间,冷却时间过长没有必要,不仅降低生产效率,对複杂製件还将造成脱模困难,强行脱模时甚至会产生脱模应力。成型周期中的其它时间则与生产过程是否连续化和自动化以及两化的程度等有关。